R2 NEXT STAGE
The new High Efficiency outdoor units of the YNW line use a four-sided FLAT TUBE all-aluminium heat exchanger close to the top of the case near the fan. This technological and construction choice makes it possible to increase heat exchange efficiency.
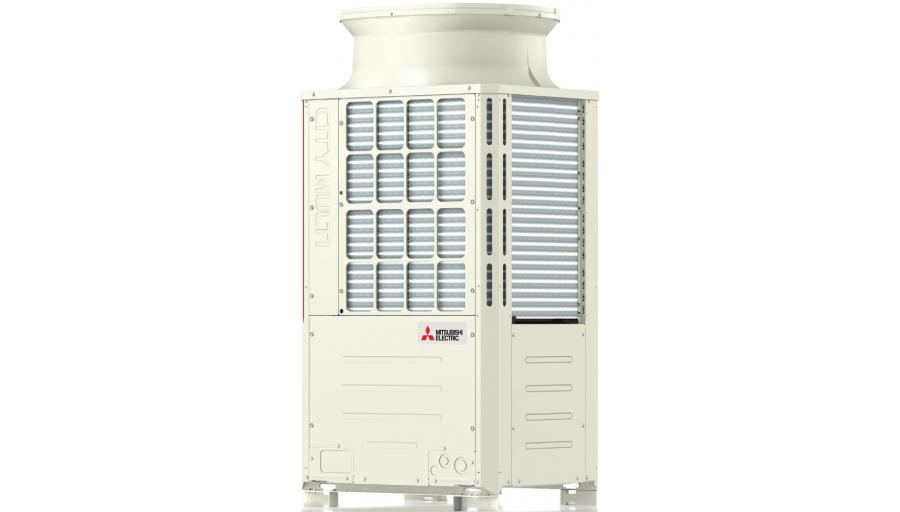
FLAT TUBE thermal exchange coil
With the new Y High Efficiency and R2 High Efficiency lines of outdoor units, Mitsubishi Electric has also introduced the new FLAT TUBE all-aluminium thermal exchange coil.
The new solution, which is covered by global patents, sets new standards for heating and cooling performance while also reducing the overall size of the machine.
The FLAT TUBE technology coil – also known as a “micro-channel heat exchanger” – consists of three components: the flat tubing, the internal fins forming the micro-channels, and two refrigerant fluid collector boxes.
This type of heat exchanger was used for the first time in around 2008 in the automotive industry.
With its globally patented FLAT TUBE system, Mitsubishi Electric has further developed this technology to offer even more advantages.
Unparalleled quality, efficiency and product integrity are the tangible results of a production process based on a single brazing stage instead of the 200-300 manually brazed individual connections necessary with a conventional copper/aluminium coil.
Moreover, the FLAT TUBE heat exchanger requires a smaller charge volume than a conventional bi-metal coil, as the microchannels limit the available volume for the refrigerant fluid while also creating a larger thermal exchange surface area.
Weather resistance is a key factor for the heat exchanger coil, as it is perhaps the component that is most exposed to the harmful effects of the atmosphere.
Here too, the FLAT TUBE coil outperforms other solutions: the single component in aluminium only is far less susceptible to corrosion than a conventional bi-metal coil in copper and aluminium.
As if that were not already enough, the direct expansion coil of the new Y High Efficiency and R2 High Efficiency lines outdoor units receive a special galvanic treatment with sacrificial zinc anodes to further prevent any possibility of corrosion, while a waterproofing treatment protects the copper pipes connecting the heat exchanger coil to the refrigeration circuit against electrolytic corrosion.
A special version (denominated -BS) may be ordered for installations in highly saline conditions or coastal zones, which is specifically designed for these applications.
Single module
Energy saving
Energy efficiency has been further improved compared to YLM units and now hits top of the range performance values. SEER values have been raised by 139% (P500) compared to the previous model and SCOP values by 49% (P300 and P500). This allows the new YNW units to consume less energy in both cooling and heating. All year-round saving.
Advanced “Low Noise” function
“Low noise” mode can now be selected from five different settings: 85%, 70%, 60% and 50% (values referring to fan speed). Noise reduction is directly configurable from the control board of the outdoor unit. Different settings can be selected based on the installation requirements (in applications with special noise constraints).
New fan blade profile
The new YNW series fan has been completely redesigned to match the new four-sided battery. The profile of the fins has been optimised to minimise fluid flow losses.
New BC distributor
Increased number of connections (for systems with BC SUB distributor) and increased geometric limits.
In the R2 heat recovery systems of the new YNW line, up to 11 BC SUB distributors can be connected to the BC Main distributor, thus allowing greater flexibility of configuration.
The adoption of the new architecture allows a reduction of the refrigerant charge in the system.